උණුසුම් ඩිප් ගැල්වනයිස් කිරීමවානේ සහ යකඩ විඛාදනයට ලක් කිරීම සඳහා පුළුල් ලෙස භාවිතා කරන ක්රමයකි. මෙම ක්රියාවලියට උණු කළ සින්ක් ස්නානයක ලෝහය ගිලී යන අතර එමඟින් ශක්තිමත්, ආරක්ෂිත ආලේපනයක් සාදයි. ගැල්වනයිස් කරන ලද ලෝහ මලකඩවලට බෙහෙවින් ප්රතිරෝධී වන අතර රළු පාරිසරික තත්ත්වයන්ට ඔරොත්තු දිය හැකිය. කෙසේ වෙතත්, ප්රශස්ත ප්රති results ල ලබා ගැනීමෙන් නිශ්චිත අවශ්යතා සහ හොඳම භාවිතයන් පිළිපැදීමයි. මෙම ලිපිය උසස් තත්ත්වයේ හා කල් පවත්නා ප්රති come ල සහතික කිරීම සඳහා උණුසුම් ඩිප් ගැල්වනයිස් කිරීම සඳහා අත්යවශ්ය අවශ්යතා සොයා බලයි.
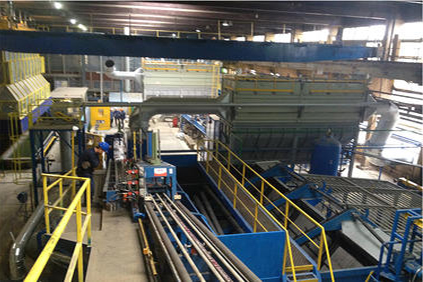

1. ද්රව්යමය තේරීම
උණුසුම් ඩිප් ගැල්වනයිස් කිරීමේ පළමු අවශ්යතාවය වන්නේ සුදුසු ද්රව්ය තෝරා ගැනීමයි. මෙම ක්රියාවලිය සඳහා සියලුම ලෝහ සුදුසු නොවේ. සාමාන්යයෙන්, වානේ සහ යකඩ ප්රාථමික අපේක්ෂකයින් වේ. ලෝහයේ සංයුතියෙහි ගුණාත්මක භාවයට සැලකිය යුතු ලෙස බලපායිගැල්වනයිස් කිරීම. නිදසුනක් වශයෙන්, සිලිකන් සහ පොස්පරස් වැනි මූලද්රව්ය ස්විට්සෙල් හි ඇති මූලද්රව්ය තිබීම සින්ක් ආලේපනයේ thickness ණකම හා පෙනුමට බලපායි. එබැවින් ස්ථාවර ප්රති .ල ලබා ගැනීම සඳහා පාලිත හා දන්නා රචනා සහිත ද්රව්ය තෝරා ගැනීම ඉතා වැදගත්ය.
2. මතුපිට සකස් කිරීම
මතුපිට සකස් කිරීම විවේචනාත්මක පියවරකිඋණුසුම් ඩිප් ගැල්වනයිස් කිරීමක්රියාවලිය. ලෝහ මතුපිට තෙල්, ග්රීස්, මලකඩ සහ මෝල් පරිමාණය වැනි අපවිත්ර කිරීම් වලින් පිරිසිදු හා නිදහස් විය යුතුය. ඕනෑම අපද්රව්ය ඕනෑම අපිරිසිදුකමක් මගින් සින්ක් නිසි ලෙස පිළිපැදීම දුර්වල ලෙස ක්රියා කිරීම වළක්වා ගත හැකිය. මතුපිට සකස් කිරීම සඳහා සාමාන්යයෙන් අදියර තුනක් ඇතුළත් වේ:
- අංශභාගය: ක්ෂාරීය විසඳුම් හෝ ද්රාවක භාවිතා කරමින් කාබනික අපවිත්ර ද්රව්ය ඉවත් කිරීම.
- අච්චාරු දැමීම: ආම්ලික විසඳුම් භාවිතා කරමින් මලකඩ හා පරිමාණය ඉවත් කිරීම, සාමාන්යයෙන් හයිඩ්රොක්ලෝරික් හෝ සල්ෆියුරික් අම්ලය.
- චතුරස් කිරීම: උණු කළ සින්ක්හි ගිල්වීමට පෙර ඔක්සිකරණය වැළැක්වීම සඳහා ප්රවාහමය විසඳුමක්, බොහෝ විට සින්ක් ස්ටෝමියම් ක්ලෝරයිඩ් භාවිතා කිරීම.
නිසි පරිදි මතුපිට සකස් කිරීම ලෝහය සහ සින්ක් ආලේපනය අතර ශක්තිමත් බැඳීමක් ඇති කරයි, ගැල්වනයිස් කිරීමේ කල්පැවැත්ම සහ effectiveness ලදායීතාවය වැඩි දියුණු කරයි.
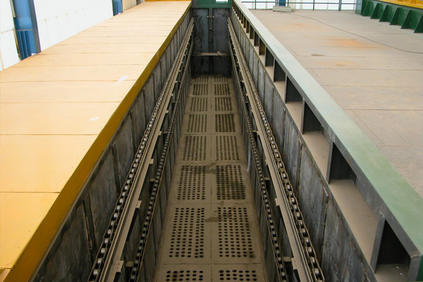
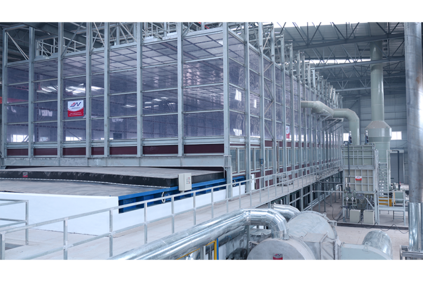
3. බාත් සංයුතිය සහ උෂ්ණත්වය
සින්ක් ස්නානයෙහි සංයුතිය හා උෂ්ණත්වය උණුසුම් ඩිප් ගැල්වනයිස් කිරීමේ ක්රියාවලියේ තීරණාත්මක සාධක වේ. සින්ක් ස්නානය තුළ අවම වශයෙන් 98% පිරිසිදු සින්ක් අඩංගු විය යුතු අතර, ආලේඛ, ඊයම් සහ ඇලුමිනියම් වැනි මූලද්රව්යයන්ගෙන් සමන්විත මූලද්රව්යයන්ගෙන් සමන්විත වේ. නාන උෂ්ණත්වය සාමාන්යයෙන් 820 ° F සහ 860 ° F (438 ° C සිට 460 ° C දක්වා) පරාසයක පවතී. ඒකාකාර හා උසස් තත්ත්වයේ ආලේපනයක් ළඟා කර ගැනීම සඳහා නිවැරදි උෂ්ණත්වය පවත්වා ගැනීම අත්යවශ්ය වේ. අපගමනය නිසා අසමාන thickness ණකම, දුප්පත් මැලියම් සහ මතුපිට රළුබව වැනි අඩුපාඩු ඇතිවිය හැක.
4. ගිල්වීමේ කාලය
සින්ක් ස්නානයෙහි ගිල්වීමේ කාලය තවත් විවේචනාත්මක පරාමිතියකි. එය thickness ණකම හා ප්රමාණය මත රඳා පවතීලෝහ ගැල්වනයිස් කිරීම. සාමාන්යයෙන්, ලෝහය ස්නානය උෂ්ණත්වයට ළඟා වන තෙක් ගිලී ඇති අතර සින්ක් වානේ සමඟ ලෝහමය බැඳීමක් ඇති කිරීමට ඉඩ සලසයි. අධික ලෙස ගිල්වීම අධික ආලේපන thickness ණකමකට තුඩු දිය හැකි අතර, යටින් පවතින අතර ගිල්වීම හේතුවෙන් ප්රමාණවත් ආරක්ෂාවක් නොලැබේ. එබැවින් අපේක්ෂිත ආලේපන thickness ණකම සහ ගුණාත්මකභාවය ළඟා කර ගැනීම සඳහා ගිල්වීමේ කාලය පිළිබඳ නිරවද්ය පාලනය කිරීම අවශ්ය වේ.
5. පශ්චාත් ගැල්වනයිස් කරන ප්රතිකාර
ලෝහය ඉවත් කළ පසුසින්ක් ස්නානය, එය ආලේපන ගුණාංග වැඩි දියුණු කිරීම සඳහා පශ්චාත් ගැල්වනයිස් කරන ප්රතිකාර වලට භාජනය වේ. මෙම ප්රතිකාර මගින් සින්ක් ආලේපනය ඉක්මනින් සුව කරන්න. මීට අමතරව, සුදු මලකඩ සෑදීම වැළැක්වීම සඳහා පානිකි පෙළගැස්ම යෙදිය හැකිය, නැවුම්ව ගැල්වනයිස් කරන ලද මතුපිටින් ඇතිවිය හැකි විඛාදනයක්. ආලේපන අඛණ්ඩතාව පවත්වා ගැනීම සඳහා ගැල්වනයිස් කරන ද්රව්ය නිසි ලෙස හැසිරවීම හා ගබඩා කිරීම අත්යවශ්ය වේ.
6. පරීක්ෂා කිරීම සහ තත්ත්ව පාලනය
අවසාන වශයෙන්, සාර්ථකව පරීක්ෂා කිරීම සහ තත්ත්ව පාලනය යනු සාර්ථකත්වය සහතික කිරීම සඳහා යඋණුසුම් ඩිප් ගැල්වනයිස් කිරීමක්රියාවලිය. පරීක්ෂාවන් සාමාන්යයෙන් දෘශ්ය ඇගයීම්, thickness ණකම මිනුම් සහ මැලියම් පරීක්ෂණ ඇතුළත් වේ. ASTM A123 / A123M වැනි ප්රමිතීන් පිළිගත හැකි ආලේපන thickness ණකම සහ ගුණාත්මකභාවය සඳහා මාර්ගෝපදේශ සපයන්න. මෙම ප්රමිතීන්ට අනුකූලව ගැල්වනයිස් කරන ලද නිෂ්පාදන අවශ්ය කාර්ය සාධන නිර්ණායක සපුරාලන අතර විඛාදනයට එරෙහිව දිගුකාලීන ආරක්ෂාවක් සපයයි.
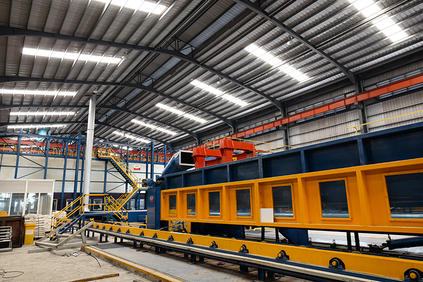
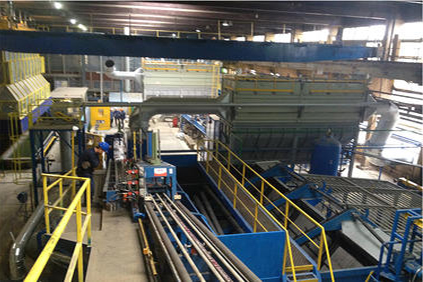
නිගමනය
උණුසුම් ඩිප් ගැල්වනයිස් යනු වානේ සහ යකඩ විඛාදනයට ලක් කිරීම සඳහා method ලදායී ක්රමයකි, නමුත් එයට නිශ්චිත අවශ්යතා විස්තර කිරීම සහ පිළිපැදීම සඳහා ඉතා සූක්ෂම අවධානය යොමු කිරීම අවශ්ය වේ. බාත් සංයුතිය, ගිල්වීමේ කාලය සහ පශ්චාත් ගැල්වනයිස් කරන ප්රතිකාර සඳහා ද්රව්යමය තේරීම සහ මතුපිට සකස් කිරීම. උසස් තත්ත්වයේ හා කල් පවතින ගැල්වනයිස් කළ ආලේපන සාක්ෂාත් කර ගැනීම සඳහා සෑම පියවරක්ම තීරණාත්මක කාර්යභාරයක් ඉටු කරයි. මෙම හොඳම භාවිතයන් අනුගමනය කිරීමෙන් හා දැඩි තත්ත්ව පාලනය පවත්වා ගැනීමෙන් නිෂ්පාදකයින්ට ඔවුන්ගේ ගැල්වනයිස් කරන ලද නිෂ්පාදන ප්රශස්ත කාර්ය සාධනයක් හා දීර් onge ායුෂ ඉදිරිපත් කරන බවට සහතික විය හැකිය.
පශ්චාත් කාලය: සැප්තැම්බර් -18 18-2024